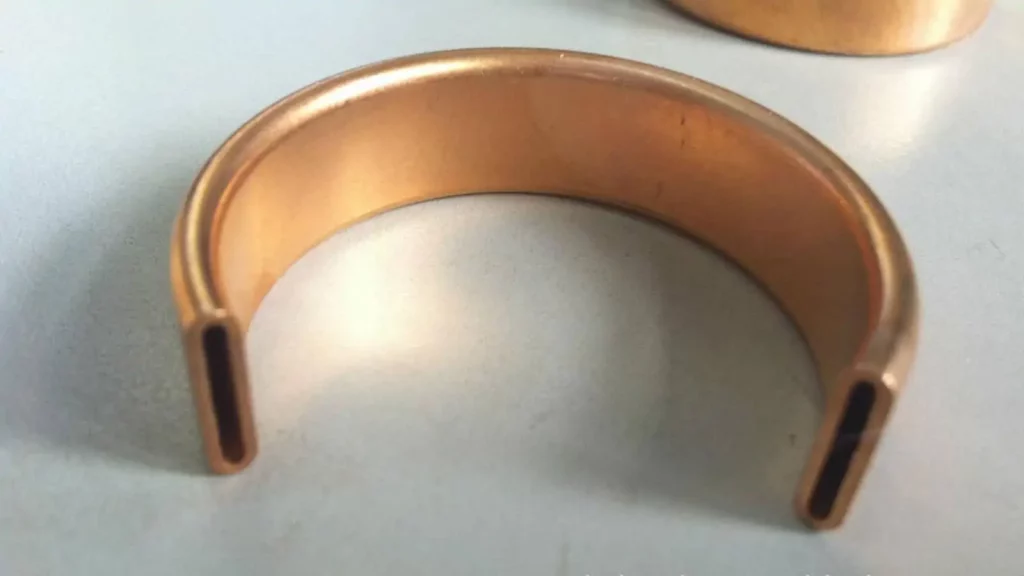
What is bourdon Tube?
The Bourdon tube is an elastic-sensitive element that uses the bending change or torsion deformation of the tube to measure the pressure, also known as the spring tube. One end of the Bourdon tube is fixed and one end is movable, and its cross-sectional shape is oval or flat. The non-circular section of the tube gradually expands into a circular shape under the action of its internal pressure, and at this time, the movable end produces a displacement in a certain relationship with the pressure. The movable end drives the pointer to indicate the size of the pressure. The most commonly used Bourdon tube is C type, in addition to spiral type, C type combination, twist type, and other types. The material of the Bourdon tube is copper-based or iron-based alloy. Compared with other pressure sensitive elements, it has lower sensitivity, and is often used to measure larger pressures, and is often used in combination with other elastic elements.
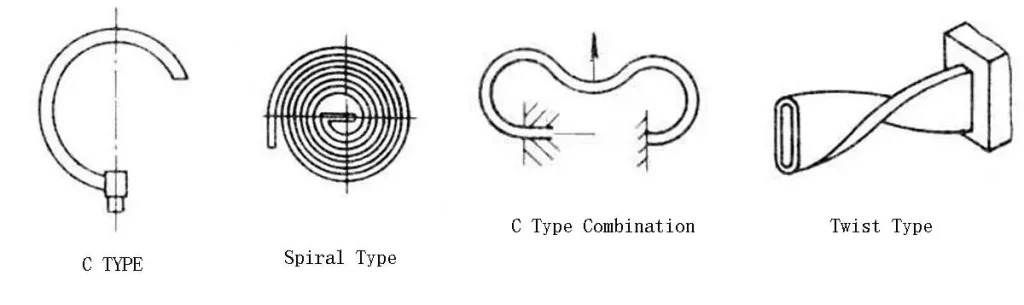
How Bourdon Tubes Work
The elastic deformation of the Bourdon tube converts the elastic deformation of the Bourdon tube into a rotary motion through the conversion mechanism of the movement in the watch, causing the pointer to deflect to display the pressure in the pressure gauge.
The end displacement of the Bourdon tube can be directly displayed by a displacement measuring device. For example, the indicator of the end driving the potentiometer, the movable iron core of the differential transformer, etc. can directly display the displacement. People can improve the performance of the Bourdon tube sensor and regulator by selecting materials, but the size design of the Bourdon tube can only be approximated by experience in the past. The Bourdon tube of elliptical section or flat round section deforms when subjected to pressure p, which reduces the ratio of the length and the short radius of the tube cross-section a/b, and the radius of curvature of the Bourdon tube increases, so the free end of the tube is displaced.
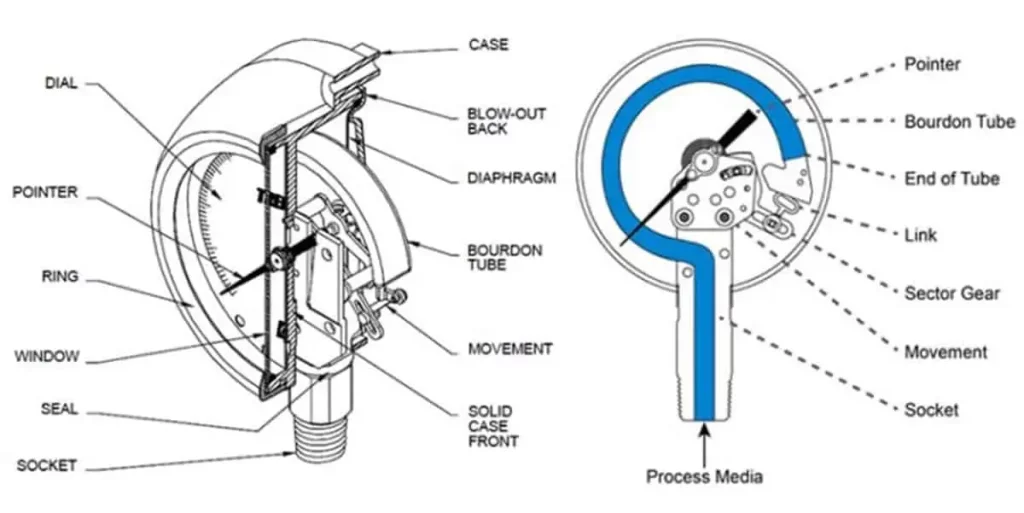
Manufacturing of Bourdon Tubes
Continuous exercise due to pressure changes can cause fatigue failure. Tiny defects on the surface of the tube will expand and deepen, and eventually cause the tube to fail. Non-metallic impurities, surface scars, carburizing or decarburization, rough or corroded surfaces, traces of defects and uneven wall thickness, all of which can cause malfunctions. Special attention should be paid to the quality of the tube blank, the process and the specifications required for various purposes. But some of the basic requirements are common requirements of all instrument users. The steel used for wool should be produced through a smelting furnace that can strictly control impurity. To prevent surface decarbonization, especially for thin-walled pipes, because surface decarbonization will reduce fatigue resistance. Fatigue Resistance Recent studies have found that the fatigue resistance of the Bourdon tube made of materials melted in a vacuum has been improved. Compared with the nickel-Span tube smelted in the air, the former is much more durable than the latter in terms of fatigue damage (the anti-damage period is extended by 12 % To 59%). The material smelted in vacuum contains approximately half of the oxide impurities of the same alloy smelted in air .
The ideal Bourdon material should be easy to manufacture, convenient to weld, and stable for a long time; it can resist corrosion and is not affected by temperature changes. It must also be the same as the processed pipe parts. Such an ideal material does not exist, so it can only be selected from its ease of processing and performance. According to the method of hardening, the metal Bourdon element must be elastic, regardless of whether this property is obtained from cold work hardening or heat treatment. The alloys used are classified according to the necessary treatments for the required properties and the degree of quenching, which can be summarized into three categories: cold work hardening, precipitation hardening, and heat treatment (quenching and tempering)
Only two of the three dimensions (OD, ID, wall thickness) can be selected when processing Bourdon belts. When forming the tube, it is best to indicate the OD of the short axis, and no tolerance is required for the long axis. In order to achieve the desired pressure deflection gradient, a tolerance is proposed for the weight of each straw. The size of the short axis is more important than the long axis when controlling the pressure deflection gradient. If the tolerance of the long axis is not very tight, the short axis can be restricted to a very tight tolerance. In fact, the general change on the short axis in a flat or elliptical Bourdon tube is only 1/3 of the long axis. The tolerance of the arc radius of the major axis does not need to be noted, because it is uncontrollable and is not important to the inherent characteristics of the pipe. Note that the tolerance of the short axis OD relative to the increase in the volume of the tube remains almost unchanged, while the tolerance of the long axis ID has increased significantly